Automotive manufacturers often face a difficult challenge in the production of their plastic parts. For decades, manufacturers have used injection molding to manufacture plastic components. Injection molding can be effective for large quantity jobs. However, it presents a number of issues for small volume manufacturers. It can often be costly to create a new mold. Those costs can make it prohibitive to run small jobs. That may limit a manufacturer’s ability to innovate and try new designs.
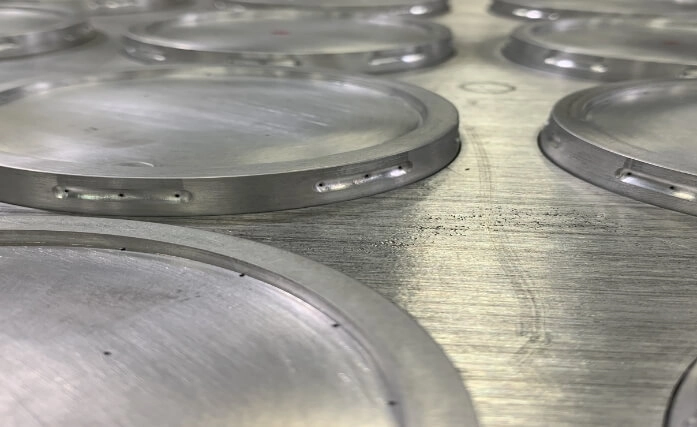
Here at Deufol, we offer an alternative production method that gives manufacturers more flexibility and greater cost efficiency. It’s called thermoforming, and it’s a unique process that allows us to create molds at a fraction of the price of injection molding. That helps manufacturers run small jobs, experiment with new designs, and better manage their capital.
There are a number of companies that offer thermoforming solutions. However, it’s important to work with a thermoforming company who will act as a true partner in your business. You want a thermoforming partner who can not only produce your parts, but also provide you with engineering and consulting services to improve quality, reduce cost, and meet your goals.
That’s our approach here, and that approach recently helped many electric vehicle manufacturers improve their quality and margins when manufacturing certain applications. Below is a recap of how we helped these manufacturers. If you’re facing a unique challenge producing your plastic applications, it may be time for you to consider a new thermoforming partner.
A Manufacturer’s Recurring Quality Challenge
The manufacturer produced plastic components for automobiles. The components had two mounting tabs used to install the part in the car. Unfortunately, there was a recurring issue involving these tabs. Although the product was produced to specifications, the tabs broke on a regular basis.
This problem obviously caused issues for the manufacturer. There was the cost of replacing the broken components. And the quality issues had an impact on their project timeline. The manufacturer spoke with our thermoforming team and expressed their desire to find a solution.
An Innovative Solution Driven by Partnership
Deufol’s thermoforming engineers analyzed the issue to identify the root cause of the problem. They determined that the material used to produce the component wasn’t durable or flexible enough to support the tabs. Thus, the tabs were bending in a way that caused cracks and even complete fractures.
Our team contacted the manufacturer of the thermoforming material. Together, Deufol’s engineers worked with the manufacturer’s engineers to create an alternative material that included additives to boost strength and flexibility.
We then created prototypes of the new component and tested it in our facility and at our customer’s facility. The result was a more durable component that didn’t have any of the cracking or breaking issues. As a bonus, the new material was actually less expensive than the previous material. That meant the electric vehicle manufacturer got better quality products at a reduced price.
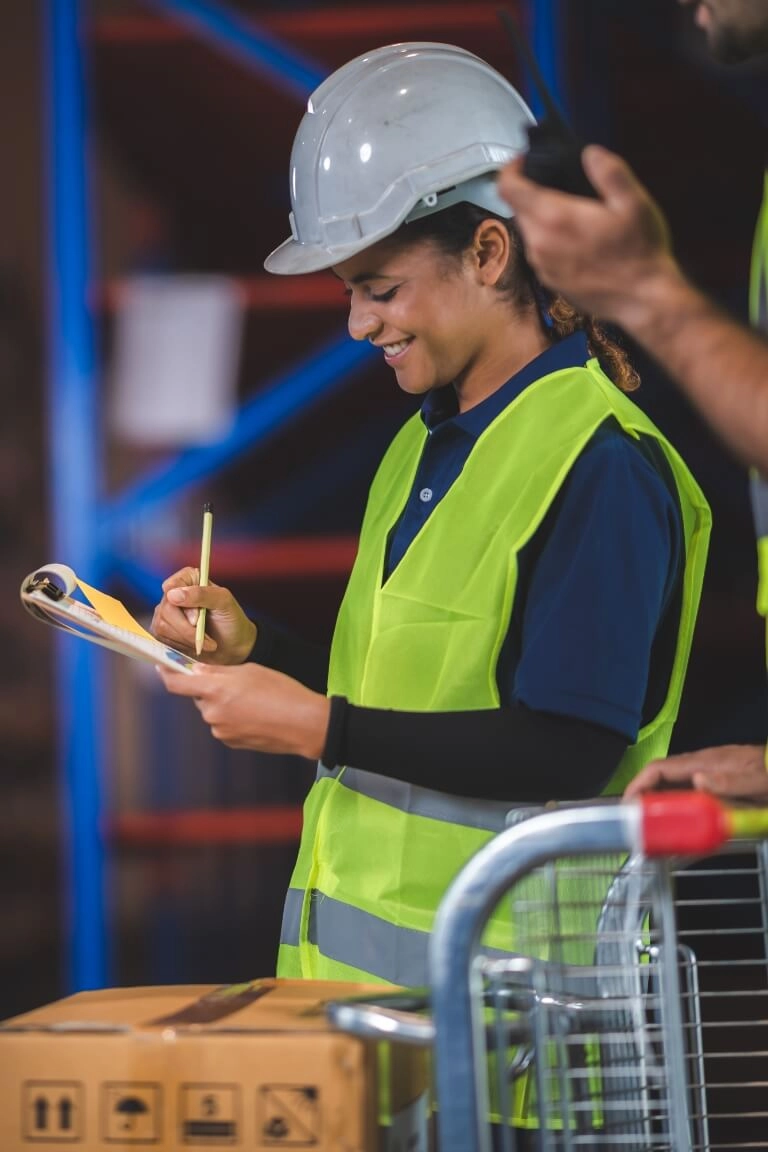
Thermoforming can be an effective solution for plastic applications manufacturers. However, as is the case in any manufacturing process, challenges and issues can arise. It’s important to work with a thermoforming partner who has engineers, consultants, and partnerships available to help you resolve your biggest challenges.