As part of our latest blog article series, we feature the largest and equally most extraordinary DEUFOL packaging projects. This article is about the packaging of a 251-tons plug-and-play compressor from our long-term customer Siemens. From the preparation through the entire packaging process up to the final transport.
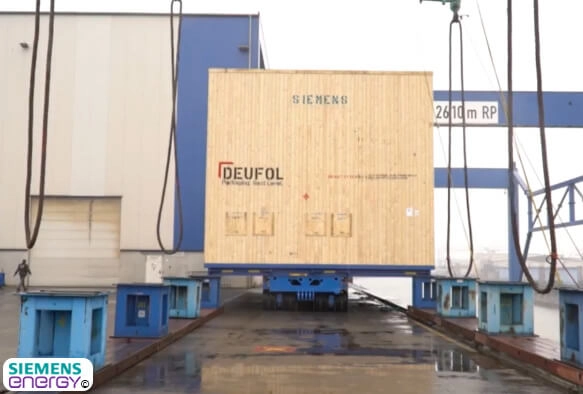
The planning of a 251 tons packaging project
Siemens, a global corporation with a focus on electrification, automation and digitalisation, contacted us in 2019 with probably one of the heaviest goods to be packed in the history of DEUFOL. A 251-tons plug-and-play compressor had to be packaged professionally and, above all, safely for transport to Korea. A challenge that would not be realisable without careful planning and consideration of possible risks. Therefore, the first step was to define the exact transport and packaging requirements together with Siemens. After successful coordination and well thought-out planning, an expert team of packaging professionals was then sent to the Siemens location in Duisburg to take over the entire handling directly on site.

Mit dem Laden des Videos akzeptieren Sie die Datenschutzerklärung von YouTube.
Mehr erfahren
Since a packaging project of this size is a rarity even for DEUFOL, every step of the assembly process had to be precisely tailored. This was the only way to ensure that the plug-and-play compressor to be packaged would arrive safely at the right destination. The first step was therefore to professionally assemble a steel floor construction that formed the foundation of the packaging. This was then preserved with sufficient foil to protect the floor from damage caused by the weather. The 251-tons machine was then placed on the steel floor with the utmost care and the individual components were preserved again in a process lasting several hours. Finally, another preservation was carried out using the VCI process, which covered the entire machine.
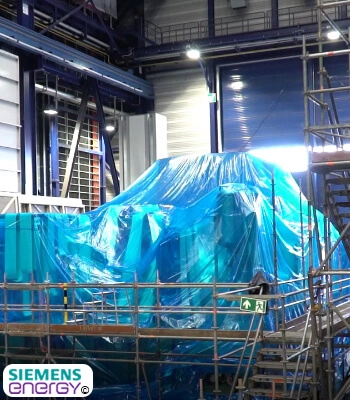
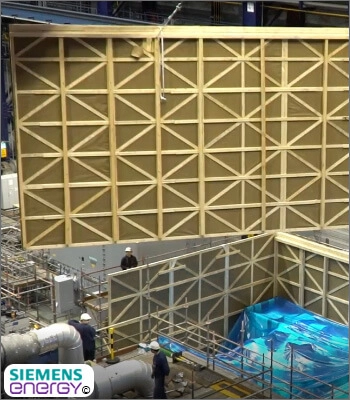
Detailed application of the side panels and Box closure
After the successful preparation of the packaging, the next step was the assembly of the side walls. These had to be precisely constructed in detail and from several segments in advance and then, like the preservation cover, placed in position with the appropriate cranes. The box lid was also assembled in place from several segments.
Creation of the lashing points and final box marking
The last challenge in the packaging process was to create the various lashing points on the crate. These had to be positioned precisely to ensure that no damage was caused to the machine or the packaging during the transport route and the high G-forces that occur in the process. The final crate marking ensures clear identification of the package on the transport route and at the receiving location. The attached DEUFOL logo then provided the appropriate recognition value.
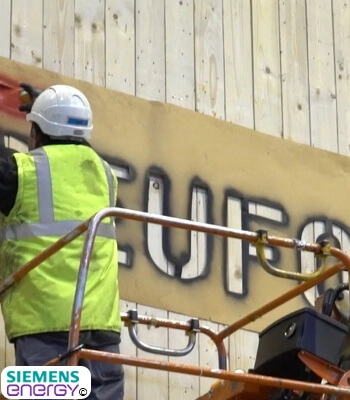
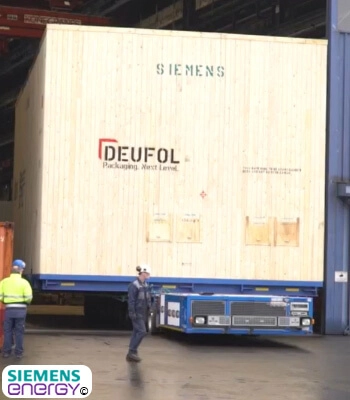
Final loading and transport to the harbour wall
After the entire packaging process was completed, a modular transport platform (SPMT – self-propelled transporter from the Spedition Kahl) took over the short but nevertheless very challenging transport to the harbour wall. In the first step, the SPMT had to be placed exactly in the right position under the machine in order to transport the 251-tons crate away. Every meter covered was closely monitored by our team in order to avoid any potential collisions.
Finally, the machine was loaded onto the inland vessel by a floating crane that had been specially brought to the site. The barge then sailed the same day towards Antwerp, where the package was again transferred to a vessel and finally transported on to Korea.
Your partner for all aspects of heavy cargo packaging
Are you also looking for a suitable contact for heavy goods packaging of any kind? Then you’ ve come to the right place! Whether for rail, ship, air freight or truck transport, no challenge is too big or too difficult for DEUFOL. We will be pleased to answer all your open questions on the topic of heavy goods packaging in an individual consultation.